Manual
CMMs
Starrett utilizes the exact rigid machine
frame design and materials for its manual line of
CMMs as its Direct Computer Controlled versions. No
area is compromised with our manual machines. The same
quality scales and air bearings are used throughout the
entire machine. Starrett manual machines also incorporate
continuous, full-travel fine feed mechanisms with axis
locks built in.Direct
Computer Control CMMs
In addition to the above prerequisites
for both Manually operated CMMs and Direct Computer
Controlled (DCC) CMMs, additional features are
important for DCC style machines.
Drive System
Starrett uses friction drives exclusively
on all three axes of every DCC machine that is produced.
These drives incorporate a direct shaft drive to a
precision drive band that totally eliminates hysteresis
(backlash). This is a true "Zero Backlash
System." (See drawing shown below.) When dealing
with highly tuned DC servo-controlled motors, hysteresis
in the drives and the machine frame cannot be tolerated
for maximum positioning accuracy and repeatability. These
drives are very low friction and induce minimum vibration
into the machine. This eliminates the reciprocating shaft
that induces vibration into the machine. This is commonly
found with ball screw or lead screw drives. We also
eliminate the hysteresis that is almost impossible to
remove from the screw drives.
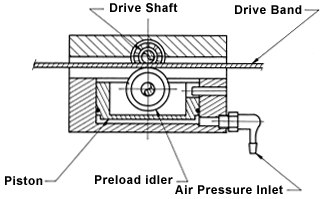
Sectional view of the
Friction Band Drive mechanism.
In addition, Starrett incorporates a Z-axis drive
isolation system on all of its DCC machines. The drive
receives all of the forces of the cables and motor system
and runs on an independent linear guideway which is
aligned with the Z-axis. When the drive moves up and
down, the linear forces are transmitted through a stiff
air bearing system to the Z-axis ceramic ram. This
totally eliminates the Z ram from the machine frame,
which isolates all lateral forces resulting from cables
and drive system misalignments. Ultimately the ram is
prevented from being deflected, which would adversely
affect linear straightness.
DCC Controller and
Hardware
The positioning of a DCC CMM is
accomplished by driving the motors of the CMM axes to the
right location. This requires an efficient communications
protocol between the controller and the CMM scales so
that the proper information is current and precise. This
information must be updated "on-the-fly."
To efficiently meet this requirement, Starrett developed
a proprietary CMM interface board which is mounted
directly onto the computer system motherboard. This
direct communications link insures that not only an
efficient and reliable link is established but the speed
of information and message passing is limited only by the
CPU processing speed.
Positioning Accuracy
It is not only important to produce
accurate measurements, it is also important to deliver
the probing system to an accurate position prior to
contact with the object being measured. This will ensure
that the MEASUREMENT point is always as accurately
collected as possible. It will also ensure the ability to
position the machine to an accurate location for
difficult-to-access positions or into tight locations.
Tunneling Accuracy
This ability to drive in as straight a
line as possible between the last
position and the next position
will not only insure collision-free motion but it will
also improve speed and throughput performance.
|